記事: 変化の時代に映える「錦山釜」【第一話】
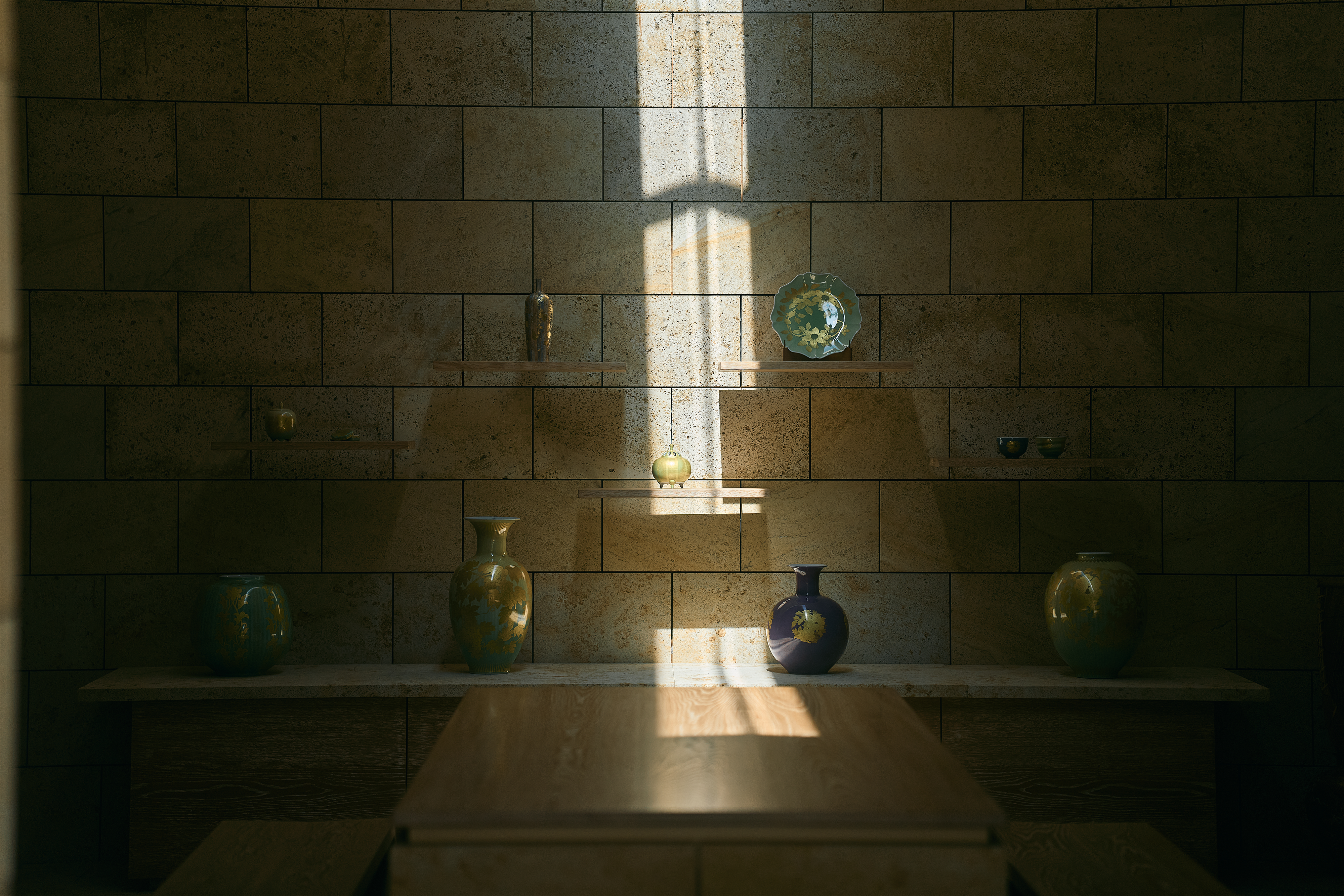
変化の時代に映える「錦山釜」【第一話】
伝統と挑戦の現在地点
一世紀以上にわたって窯の火を絶やさず、九谷焼の上絵付を専業としてきた「錦山窯」。洋絵具による上絵付と金彩を組み合わせた「彩色金襴手」が特徴で、その繊細で鮮やかな絵付けは日本の伝統工芸にあってひときわ存在感が際立ちます。伝統を受け継ぎながらも新しい可能性に挑む錦山窯四代の吉田 幸央さんに、九谷焼の現在と未来について伺いました。

そもそも九谷焼とはなにか
石川県無形文化財に指定されている九谷焼の発祥地は加賀国江沼郡九谷村で、現在の石川県加賀市山中町九谷村にあたります。しかし、この窯は1730(享保15)年頃に突如として廃窯。窯が閉じられた経緯については諸説あり、さまざまな研究が進むもののいまだその理由は定かではありません。この時期に焼かれた九谷焼は現代の久谷と区別して「古九谷(こくたに)」と呼ばれています。
その後およそ80年の月日が経ち、加賀では九谷焼を再興する動きが強まりました。京都より文人陶工の青木 木米が招かれ、1807(文化4)年に金沢の卯辰山に「春日山釜」を築いたことで加賀久谷の歴史が始まります。ほどなくして能美郡花坂村にて古九谷の原料に近い花坂陶石が発掘され、近隣に「若杉窯」が開かれます。以来、各地で次々に新しい窯が開かれていきました。これらは「再興久谷」と呼ばれ、伝統的な技法をベースとしながらも創意工夫をこらした新しい作風を生み出します。明治時代に入ると色絵や赤絵細描を学んだ九谷 庄三が洋絵具を取り入れ、上絵付けに金彩を施す「彩色金襴手」を確立。これが1873(明治6)年のウィーン万博で「ジャパン・クタニ」として世界に広まり、一世を風靡しました。この鮮やかな色彩と埋め尽くさんばかりの装飾性こそ九谷焼の魅力といえるでしょう。作家や窯元ごとに違う多彩な表情、繊細にして大胆な色絵装飾のすばらしさは、日本の伝統工芸においても白眉といえます。

絵付けの職人による作業はおもわず息を止めてしまう。

錦山釜の作品に使用するカラーパレット。

いま、もっともモダンな九谷焼の一つといえる。

工房では作家の仕事場と職人の仕事場で分かれる。
系譜からみる「錦山釜」
錦山釜は石川県小松市高堂町にある九谷焼の上絵付を専業とする窯元です。初代𠮷田 庄作のルーツは、赤絵金襴手の発展に寄与した佐野釜の斉田 伊三郎に学び、久谷 庄三の陶画工として腕を磨いた小酒 磯右衛門に行き当たります。その系譜であり、庄作の直接の師である田中 英亮は九谷焼の最盛期ともいえる明治時代に独立し、多くの徒弟や職人を雇って絵付業を大きく広げた人物。英亮の下で作陶を学んだ庄作は、その後金沢で金粉を撒く「錦振り」という技法を習得。金の扱いに秀でた絵付け師として1906(明治39)年に、現在の高堂町に「錦山釜」を立ちあげます。細密な色絵に金を施す多彩な技法は、後に「高堂絵付」と呼ばれるようになります。1933(昭和8)年、庄作の末弟だった清一が28歳で錦山釜の二代目となり、花鳥風月を取り入れた「金彩細描画」や、金が配給制となった戦時中に手掛けた「青手久谷」など、新しいデザイン技法を確立。各種の美術展や工芸展に入賞しました。
わずか36歳で夭逝した清一に代わり、現在の三代目である𠮷田美統(みのり)さんが錦山釜を継ぎます。1960(昭和30年代にはデザインを学び、1970(昭和40)年代には自身の作家活動だけでなく同世代の仲間と「旭釜」という共同釜を立ちあげ、ハンドメイドの商業化を試みます。製造においても九谷焼の窯で初めて電気窯に電気制御盤を導入するなど、新しい技術も積極的に取り入れていきました。その後、花や蝶などの具象をモチーフとする「釉裏金彩」を確立させたことで、国指定重要無形文化財保持者(人間国宝)に認定され、いまなお作家として活躍しています。
そして、その伝統と革新の姿勢は現在、四代目の𠮷田幸央(ゆきお)さんに受け継がれ、さらなる発展を遂げようとしています。幸夫さんは水彩画のような立体感のある色の美しさ、金の華やかさをモダンに表現する独自の世界観を確立。彩色金襴手のさらなる可能性を追求しています。現在の九谷焼はその技法やデザインが多岐にわたりますが、錦山釜は小松久谷の源流をたどる系譜といえそうです。

「白素地(シロキジ)」と呼ばれる絵付け前の九谷焼。

これが三代目、𠮷田美統(みのり)さんの仕事場。

年季の入った仕事道具が並ぶ。

下絵を写す際に使う椿の葉。久谷の窯元には必ず椿が植わる。

錦山釜の金は華やかなだけでなく、深い。

金箔の厚さを変えて自然の豊かな表情を出す。

こうした道具も独自に開発されたものが多い。
革新が紡ぐ伝統
錦山釜では現在、92歳の美統さんをはじめ、四代目の幸央さん、その妻のるみこさん、そして長女のみふゆさん、長男の太郎さんが作家として作品を発表しています。しかし、その作風はそれぞれ全く違うもの。錦山釜の現在地について、幸央さんに伺いました。
「現在、錦山釜では大きく二つのカテゴリに分かれて仕事をしています。ひとつはそれぞれの作家による作品で、もう一つが錦山釜としての作品です。前者はそれぞれが自分と向き合い作品を生み出していきますが、後者はみんなで色々と話し合いながら時代に相応しい作品を作りだします。
いまは家族全員が作家として活動していますが、長女も東京で仕事をしていましたし、私も若い頃は特に後を継ぐことを意識したわけではありませんでした。しかし、間近で九谷焼ができあがっていく様子を見ていて、自分も何か作ってみたくなる。他の仕事をしてみて九谷焼の良さに気付くこともあるかもしれませんし、逆に九谷焼と違うものを作ってみたくなることもあるでしょう。お互いが影響し合い、それを受け入れたり拒絶したりしながら、それぞれの作品を追求しているのです。
伝統工芸というと同じことの繰り返しのように思われるかもしれませんが、実は細かな変化や進化の積み重ねの歴史といえます。再現性を高めるために新しい道具を発明したり、効率を良くするために他の技術を取り込んで改良したり、常に変化していく。時代やテクノロジーの進化に合わせて変わっていくことで、逆にずっと変わらない部分が見えてくるような気がします。私も60歳を超え、果たして社会に必要とされるのか(笑)。でも、自分はやりたいこと、挑戦したいことがまだまだある。作家としても錦山釜としても、いま目の前にある挑戦にワクワクしているのです」

錦山釜四代目の𠮷田幸央(ゆきお)さん。

長男の太郎さん。釉薬にフォーカスした作品が特徴的。

釉薬の自然な表情から表現を模索する太郎さんの作品。

上絵付を専業としてきた窯には珍しい轆轤場。

長女のみふゆさん。作家としてだけでなく、錦山釜の広報活動も担う。

みふゆさんの作品には絵画のような九谷焼の新しい魅力を感じる。

同じ錦山釜とは思えないほど多彩な作品が生まれる。